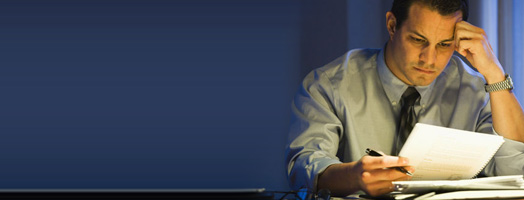
Publications
BOOKS
Performance Improvement for Healthcare
by Bahadir Inozu, Ph.D., Dan Chauncey,
Vickie Kamataris, Charles Mount
Foreword by Dr. Bob Halder, Rear Admiral, U.S. Navy (Ret)
NOVACES is proud to share with you our latest book, a pioneering guide that lays out an integrated approach for using three proven methodologies to transform hospital operations in terms of patient outcomes and experience, financial viability, and employee satisfaction. Now available at Amazon.com
WHITE PAPERS & CASE STUDIES
Browse our latest white papers and case studies for the latest insights and implementations of continuous process improvement. The information is free for download.
INDUSTRY FOCUS: DEPARTMENT OF DEFENSE / GOVERNMENT
The Commander and Continuous Process Improvement
It's About Readiness... And Leaving the Outfit Better Than You Found It
Industry Focus: Department of Defense
During the last several years, we have seen Department of Defense (DoD) organizations that have embarked on an effort to deploy Continuous Process Improvement (CPI) across their commands. In some cases, it seems that the scope of these deployments is focused on processes that span the entire command with little attention to the tactical unit level. Read more >>
Strategic Collaboration: Perspectives on Military Healthcare Quality Improvement
Industry Focus: Military Healthcare
Continuous Process Improvement (CPI) in the military healthcare system and the Veterans Health Administration (VHA) have some differences but share many similarities in their approach to quality improvement. With an emphasis on sharing best practices, the opportunity for future advances is something that can rapidly benefit both the military healthcare system and the VHA. Read more >>
PROCESS IMPROVEMENT INSIGHTS
Introducing SystemCPI: An Integrated Roadmap to Deploy and Manage Process Improvement Initiatives
Industry Focus: General
The SystemCPI roadmap – an integration of Lean, Six Sigma, and Constraints Management – simplifies management’s job by providing a systems perspective to focus improvements where they are needed to achieve enterprise-level impact. Read more >>
Apprenticing Master Black Belts
Options for Self-Sufficiency: Buy, Rent, or Grow?
Industry Focus: General
As a deployment leader, determing the best approach to grow a Lean Six Sigma program that is self-sufficient is always top of mind. Having highly qualified Master Black Belts on staff is a critical variable in the equation. Discover some of our insights on the best ways to achieve this milestone, and weigh the pros and cons of each option. Read more >>
Mentoring as a Lean Six Sigma Enabler
Using Results-Oriented Mentoring to Boost Self-Sufficiency and ROI
Industry Focus: General
There are several places to examine how a deployment evolves: alignment with strategic goals, project selection, infrastructure, selecting the right people to become involved and so forth. Yet one key area frequently overlooked is the importance of using practitioner mentoring programs as a means to reenergize a program and drive the kind of ongoing project accomplishments that support the enterprise’s needs. Read more >>
INDUSTRY FOCUS: HEALTHCARE
Perspectives on Lean Six Sigma in Healthcare: We the Patient
Industry Focus: Healthcare
As patients, we no longer accept our healthcare in its present condition. It often takes too long to start our care, test results wait times seem interminable, we’re afraid of getting an infection, our discharge process seems inefficient and the billing is confusing. Out of necessity, our knowledge about healthcare has grown markedly over the past several years. What impact will Lean Six Sigma have on healthcare? Read more >>
JumpStart: A Healthcare Case Study
Industry Focus: Healthcare
This not-for-profit hospital system in New York was looking to move forward with Lean Six Sigma. However, the leadership team knew that they did not have a deployment strategy in place to get the results they were looking for. They turned to NOVACES to help form a strategy for Lean Six Sigma deployment and build the infrastructure for a self-sufficient program. Read more >>
Laboratory Turnaround TImes in Emergency Departments
Eliminating Wasteful Steps and Bottlenecks with Lean Six Sigma
Industry Focus: Healthcare
The Emergency Department (ED) is often the primary care for many patients. Patients who are uninsured, under-insured, or those who have no primary care provider turn to a hospital's ED as a safety net to gain access to the healthcare network. Laboratory results have a cascading effect on patient throughput in today's overcrowded EDs. In this case study, Lean Six Sigma produces dramatic results for this hospital that was ready for change. Read more >>
Using TRIZ Innovation Tools in a Rapid Improvement Workshop
Industry Focus: Healthcare
A Rapid Improvement Workshop (RIW) was conducted to address coordination of patient care in the Emergency Department of a community hospital. The RIW was the result of a ProcessVSA that had focused on reduction of turn-around-time (TAT) for STAT lab tests. TRIZ innovation tools were used to implement unique visual management methods, which resulted in a 66% improvement in order-to-collect times. Read more >>
ProcessVSA: Improving Core Measure Performance for Congestive Heart Failure Discharge
Industry Focus: Healthcare
Congestive Heart Failure (CHF or HF) is a leading cause of mortality and morbidity in the US, affecting more than five million people. With the prevalence and incidence of CHF rising, the rate of hospitalization is increasing. The estimated cost of CHF in 2008 was nearly $35 billion. A readmission rate of 24.5% is a key cost driver and compelling evidence that existing approaches to managing CHF require improvement. Read more >>
Strategic Collaboration: Perspectives on Military Healthcare Quality Improvement
Industry Focus: Healthcare
Continuous Process Improvement (CPI) in the military healthcare system and the Veterans Health Administration (VHA) have some differences but share many similarities in their approach to quality improvement. With an emphasis on sharing best practices, the opportunity for future advances is something that can rapidly benefit both the military healthcare system and the VHA. Read more >>
10 Common Performance Improvement Mistakes
Lessons Learned and Observations from the Field
Industry Focus: Healthcare
Over the years, NOVACES has helped healthcare organizations across the country improve operational, financial and patient care performance. Through this journey our team documented the 10 most common mistakes hospitals make before engaging a performance improvement expert. Read more >>
INDUSTRY FOCUS: MARITIME / INTERMODAL TRANSPORTATION
Value Stream Analysis of the Voyage Planning & Scheduling Process
Industry Focus: Maritime / Intermodal Transportation
The shipping lanes of Crowley’s Liner Services Division exist primarily on the east coast of the United States, the Caribbean, and central America. On a seasonal basis, winter storms and hurricanes in the region, coupled with other operating challenges, frequently cause abrupt schedule changes to planned voyages. This had a tremendous impact on Crowley’s operations and, importantly, its customers. Learn how this Value Stream Analysis reduced the cycle time by 75% and labor costs by 90% for this critical, customer-focused process. Read more >>
Follow Us: