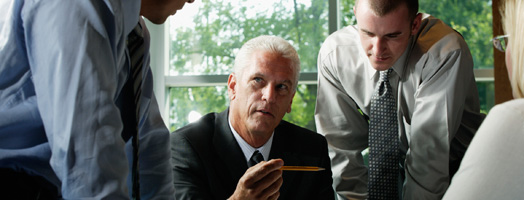
Quality Management
At NOVACES, quality is not an afterthought — it is a systematic, proactive process integrated into every stage of program delivery.
Our Quality Management System (QMS) utilizes quality audits to ensure proper implementation and reporting of scope, cost, schedule, and cross-functional program/project controls. Additionally, we employ key performance indicators (KPIs) to measure and report monthly on the performance of the program management team, sub-consultants, and project management team.
Benefits of Effective Construction Quality Control:
-
Reduced Rework: Identifying and correcting issues early in the construction process minimizes the need for costly rework later.
-
Improved Project Outcomes: Consistent quality control leads to a higher quality finished product, enhancing client satisfaction.
-
Cost Efficiency: Preventing defects and minimizing rework help optimize the project budget.
-
Enhanced Safety: Quality control practices can also contribute to improved safety standards on construction sites.
At NOVACES, implementing quality is the systematic process of monitoring and verifying that all aspects of a construction project adhere to established standards, including inspections, testing, and documentation, to ensure the final product meets design specifications and client expectations throughout the construction process; essentially, it involves actively identifying and rectifying any deviations from quality standards to deliver a high-quality project.
Key Aspects of Construction Quality Control:
-
Quality Control Plan (QCP): A detailed document outlining the procedures, inspection methods, and acceptance criteria for each construction phase to maintain quality throughout the project.
-
Inspections and Tests: Conduct regularly scheduled checks on materials, workmanship, and completed work to verify compliance with specifications, often using checklists and documented observations.
-
Quality Assurance (QA):
A proactive approach to prevent defects by implementing systematic processes, training, and quality management practices across the project team.
-
Documentation: Thorough record-keeping of inspection results, non-conformance reports, corrective actions, and other quality-related data to track progress and identify areas for improvement.
-
Subcontractor Management: Ensuring all subcontractors understand and comply with the project's quality standards through clear communication and monitoring of their work.
Key Steps in Construction Quality Control:
-
Define Quality Criteria: Establish clear and measurable quality standards for materials, workmanship, and project deliverables.
-
Develop Inspection Plan: Create a detailed plan outlining which aspects of the project to inspect, the frequency of inspections, and who will conduct them.
-
Conduct Inspections: Perform regular inspections throughout construction, documenting findings and identifying deviations from quality standards.
-
Corrective Actions: Address identified issues promptly by taking corrective actions, such as rework, material replacement, or process adjustments.
-
Closeout Inspections: Conduct final inspections upon project completion to ensure all quality requirements have been met.
Follow Us: