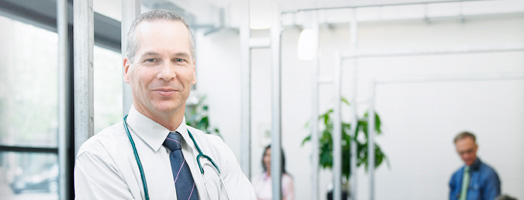
Avoid 10 Common Mistakes in Lean Six Sigma and Healthcare Performance Improvement
Part 1. Create an Inventory of Experts Right Away
Once an organization decides to begin implementing Lean Six Sigma, it’s time to think about how to make the investment produce real benefits in terms of patient satisfaction, quality and safety of care, and dollars. Developing an expert in Lean Six Sigma is a significant investment and it is commonly the first step in the journey. The tools and skills that this person must master are many, but so are the rewards that can be reaped. There are several options for training, including open enrollment courses, on-site courses, and virtual courses, and each has its pros and cons. However, don’t jump into training too early or design it to be too large a factor in the early stages of the implementation plan.
First, don’t get this confused with leadership training. It is important to educate the senior leadership team early on how methods like Lean and Six Sigma apply in healthcare – more specifically, in your hospital – and open some discussion amongst the team about how it could help to accomplish some important goals. It is not, at this point, imperative to send staff to get expert training in Lean or Six Sigma.
Many times with the initial push to train experts, an unexpected pool of resources are created who can’t get the support to complete projects or improvement workshops. This leads to confusion and poor results for important projects, or alternatively, an investment of scarce resources on projects that are not truly important to the organization. A false start for the process improvement program can set progress back significantly for those that are responsible for taking the hospital’s process improvement program to the next level.
An alternative approach that enables the hospital to properly test the concept is recommended. Select an important initiative that has proven to be notoriously difficult in the past or that has had problems with sustainability. Then proceed to put together a pilot that will enable a team from your organization to work with a healthcare Lean Six Sigma expert to apply the tools correctly and begin learning how to make it work for your organization.
The chances are that the team will learn many things about process improvement methods and tools while working hands-on with an expert. And there is a much better chance that the effort will be completed quickly and will return the expected benefits. The discoveries made by working with a process improvement expert can then be fed back to the leadership team and allow better decisions to be made about what training is right for your organization, who should attend it, and when you are ready for it.
Stay tuned for the next installment, in which we’ll explore the need to bring together the worlds of healthcare finance, quality and patient safety in “Part 2: It’s All About Quality.”
Also In This Issue:
- Improving Core Measure Performance With Lean Six Sigma: Congestive Heart Failure (CHF) Discharge Case Study
- Webinar Spotlight: SystemCPI: A Case Study
- Calendar of Events
- Get to Know Us: Vickie Kamataris, Healthcare Master Black Belt