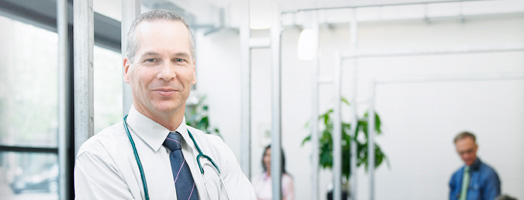
TOP 10 PERFORMANCE IMPROVEMENT MISTAKES
Part 5: The Theory of Evolution
During the mid-1980s, Lean, Six Sigma and Constraints Management (or Theory of Constraints) emerged as three schools of thought for organizations that were embracing Continuous Process Improvement (CPI). Until the late 1990s, these methodologies were like three different religions—coexisting, but completely independent of each other. However, since not every problem is a nail, a hammer is not appropriate for all problems. Leaders who are implementing CPI and performance improvement in healthcare should not struggle with the choice of which single methodology is right for the organization, but rather the vision is to enable capabilities in all of these tools and methods to evolve continuously.
Let’s Make a Deal: Door #1, Door #2, or...?
In healthcare specifically, Hospital Corporation of America (HCA) adapted Deming’s PDCA and added the FOCUS portion in the late 1980’s. This has been expanded across the entire industry over the past 20 years. Currently, Lean applications in healthcare appear to be the most popular among US and UK hospitals. Six Sigma applications closely follow. According to an ASQ survey, 53% apply Lean, 42% apply Six Sigma at some level and 37% take the hybrid approach of Lean Six Sigma [1].
On the other hand, Constraints Management applications in healthcare are at their infancy but breakthroughs are documented at hospitals in the U.K., Israel, Netherlands, and New Zealand. In fact, in the Netherlands, about one-third of all hospitals that implement a process improvement program choose Constraints Management [2].
The goal, however, is to improve performance across the organization by maximizing the quality of care and minimizing cost. This is accomplished through the identification of poorly performing processes that have the largest impact on the system’s costs and quality -- and then fixing them. Unlike a “one size fits all” approach - such as Lean only or Six Sigma only or Constraints Management only - it is more important to focus on using the right tool for the right problem at the right time to deliver faster results and greater return on investment.
It’s Not Easy!
Certainly the task of building the capabilities to apply all of these tools and methodologies is not an easy one. However, we didn’t become quality professionals because we were looking for the easiest path to early retirement. Rather, I think that we are resolved to stay the course and chip away at problems - big and small - every chance we get.
In reality, though, no matter how hard we push or how effectively we lead, there is a limit to the amount of CPI that an organization can absorb over a given period of time. So the foundation must be laid for CPI first. The strength of that foundation indicates how quickly new things can be assimilated into the CPI toolset. The organizational culture must first embrace CPI - it should have continuous improvement in it’s blood.
In the figure, you will noticethat after the foundation is laid, the corporate appetite for CPI requires that it continues to evolve. It cannot take on the flavor of the month, but instead clearly show a vision for building on the success of what came before. If leadership allows the program to look like a methodology graveyard, the organization will experience a deterioration of its CPI culture. This is why integration plays so heavily into the evolution of process improvement.
As the focus turns to new methodologies and tools, it should be carefully integrated into the existing program and communicated properly throughout the organization. Ultimately, finding the synergies is what produces huge leaps in performance and propels your organization to new levels of excellence.
Also in This Newsletter
Beyond Technology: Focus on Better Process for Supply Chain Management
WEBINAR: Taking Lean to the Next Level: A Hospital Case Study
WEBINAR: Medication Reconciliation - How One Project is Putting a Dent in One of Healthcare's Toughest Problems
Previous Issues of Performance Improvement Mistakes
Part 1: Create an Inventory of Experts
Part 2: It's All About Quality
Part 4: Boil the Ocean
References
[1] ASQ Quality Progress / 2009 August, Get Your Checkup, ASQ study looks at hospital deployment of lean and Six Sigma, by the ASQ Lean Six Sigma Hospital Study Advisory Committee.
[2] Burgess, 2009, How is Lean being applied to health? Classifying approaches to Lean implementation in the NHS.
Follow Us: